Technology
Trailblazers: Plant Prefab Models A Hybrid Fusion Of Panels, Modules
Scalability in design and construction of homes for bespoke lots, infill sites, and tracts that higher-volume producers tend to ignore gets a hub-and-spoke manufacturing and distribution platform.
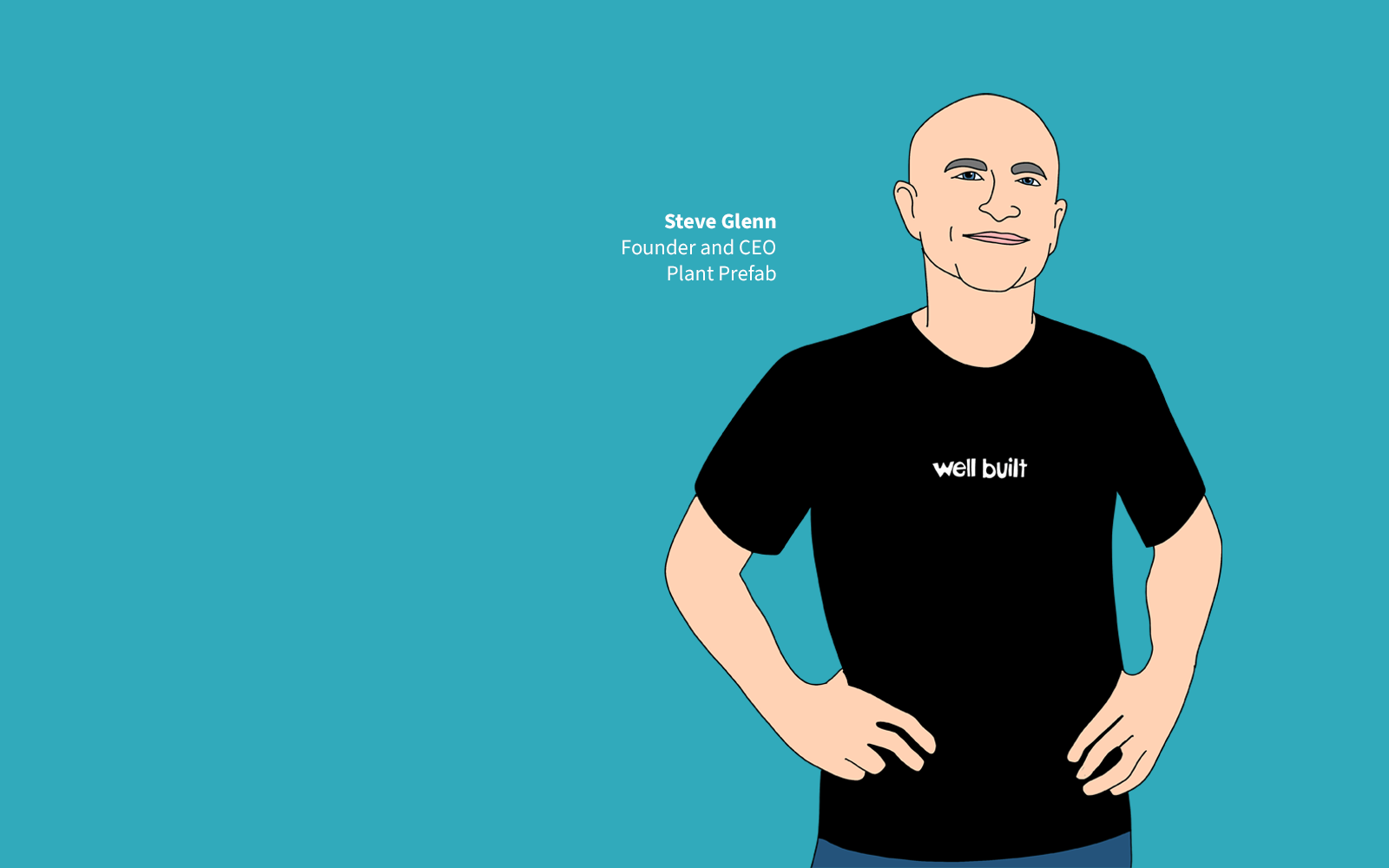
The jury's out on the ultimate severity and duration of this housing swoon.
Way smarter people than us are clocking in, with views ranging from "the worst is over," to "it will definitely get worse before it gets better," to "don't hold your breath." And way smarter people than them are probably withholding saying anything at all until there's more to go on and less that's unknowable.
For Steve Glenn and Plant Prefab, a Southern California-based future-of-housing building technology and production platform he stood up in 2016, the complexion of near-term demand is – in some ways -- moot. 2023 mapped to a late-beta early release candidate timeline for the firm's tech and production stack anyway. So, whether or not the housing market shows true green shoots midyear or not until the end of next year, or even midway through 2024, is not necessarily an existential matter.
Glenn – founder and CEO of Plant Prefab – fixates on bigger, more chronic, harder, and increasingly more urgent challenges that both preceded the Covid-and-Fed-triggered downturn of 2022, and will no doubt await us coming out of it. The challenges make for a quintfecta of urgencies that housing trailblazers like Glenn, scattered from coast-to-coast, unreasonably but unswayably view as five sides of the same coin.
- Housing attainability
- Sustainable, carbon positive, and resilient buildings
- Local adoption and support
- A recoupled and activated building talent pool
- Reignited consumer household aspiration and motivation
Housing's solutions, they bet their careers and all the capital they can lay their hands on, can not be any one of those fixes in isolation. At best, achieving one of the four goals without the other three would only amount to a fleeting accomplishment. These trailblazers work in the nexus of rapidly advancing technologies, data, machine learning, mechanical engineering, sensor-enabled automation, architecture, and code all brought literally down to earth, the dirt of a homesite and the elements of time and climate.
Glenn – like scores of serial entrepreneurs, tech company stand-outs, industrial engineers, investment and venture capital mavens currently tapping into $2 billion or more early-phase funding to – cheered with his team earlier this month on news they'd secured $42 million in Series C and other funding.
A Tech Crunch analysis notes:
Plant Prefab’s new round consists of around $30 million in equity led by Brazilian steelmaker Gerdau, as well as $12 million in debt from Silicon Valley-based Western Technology Investments and ATEL Capital. Other investors to chip in on the equity side include Tokyo-based chemical company Asahi Kasei, a Brown University alumni group and Unreasonable Collective, an entrepreneurship club. That’s in addition to early top-ups from firms like Amazon and Obvious Ventures."
The funding round, Glenn tells The Builder's Daily, will enable Plant Prefab to complete the 270,000 square-foot, multi-stack Tejon Ranch Hub facility, whose automated systems will step-change the firm's capability from a current output of 35 to 45 homes a year to a level of 800 new homes – i.e. 900,000 square feet of built environment -- annually.
In the context of the quintfecta noted above, Plant Prefab's pitchdeck doesn't claim in and of itself to be out to save the world. What it does regard as an inextricable helix is the weave between affordability, beauty, durability, and sustainability. Its governing, underlying construct evolves out of a mass customization capability that would engage a value-cycle involving architects who do best as solving for hyperlocality empowered at a modern manufacturing level to do housing at a high-efficiency, zero waste, and extended lifetime value level. A statement notes:
Plant Prefab’s data-driven processes produce 30 percent less construction waste than site-based methods, and corporate responsibility initiatives spanning everything from material sourcing to component shipping efficiency have helped the company achieve carbon-neutral operations since 2020. The Tejon Ranch Hub is being constructed to Plant Prefab’s strict environmental standards for minimal resource consumption and will be fully solar-powered. The company plans to continue scaling its sustainable housing production through a hub-and-spoke model that will eventually serve the entire continental U.S. Standardized Plant Panels will be produced at highly automated, high-volume regional hub facilities with consolidated resources, while Plant Modules will be assembled at spoke facilities that are located closer to customers to minimize shipping costs and on-site finish work."
What's different about the manufacturing processes Plant Prefab is laying out an assembly platform for is what Glenn believes is the nation's first hybrid panel and module manufacturing facility.
Using our Plant Panels as building blocks in the manufacturing process, we'll build Plant Modules to incorporate integrated building systems for bathrooms, kitchens and the like, and we'll ship flat Plant Panels for structural enclosure elements," says Glenn. Plant Prefab, he says, has built a contractual backlog that totals more than $85M and prospective business totaled more than $660 million, representing year-over-year growth of 58% and 110%, respectively. Contracts include workforce, affordable and market-rate housing spanning multifamily, single-family, single-family community and student housing developments."
The Southern California-based Tejon Ranch facility, Glenn says, will be able to leverage Plant Prefab's Rialto and Ontario, CA, factories, to serve a Western region, up and down California as far east as Colorado.
In the future, as we expand our network eastward, the spoke facilities will be consumers of the Plant Panels, and they'll to the assembly and delivery," says Glenn. "Essentially what we're doing with Plant Panels, together with our digital twin preconstruction build of each building empowers us to compress schedules, trade crew requirements, eliminate material waste, and elevate the quality of the structures and the systems."
It's not just about changing the way to build a home. It's remapping and retooling the way to build a sustainable housing company that can contribute to changing housing as an economic, social, environmental, and health solution.
MORE IN Technology
Design-Estimating Disconnects Cost Builders Time And Margin
Former builder-operators Brandon Pearson and Marcus Gonzalez share what’s broken—and how connected teams can win now and in 2030.
What Separates Homebuilders Thriving Amidst 2025’s Chaos
Builders face rising stakes to unify tech, data, and operations or risk falling behind amid affordability, insurance, and labor challenges.
Margin Mission: Homebuilders Race To Crack Inefficiency Code
Spring 2025 has fallen short of expectations. Builders are turning to integrated data systems to protect margins and prep for the next wave.