Products
Will Red Sea Disruptions Show Up In Builders' Build-Cycles Again?
Securing the right materials in the right place at the right time is crucial to accessing the right labor in the right place at the right time. Supply disruptions affect builders’ ability to use labor efficiently, leading to more challenges in getting homes built on time.
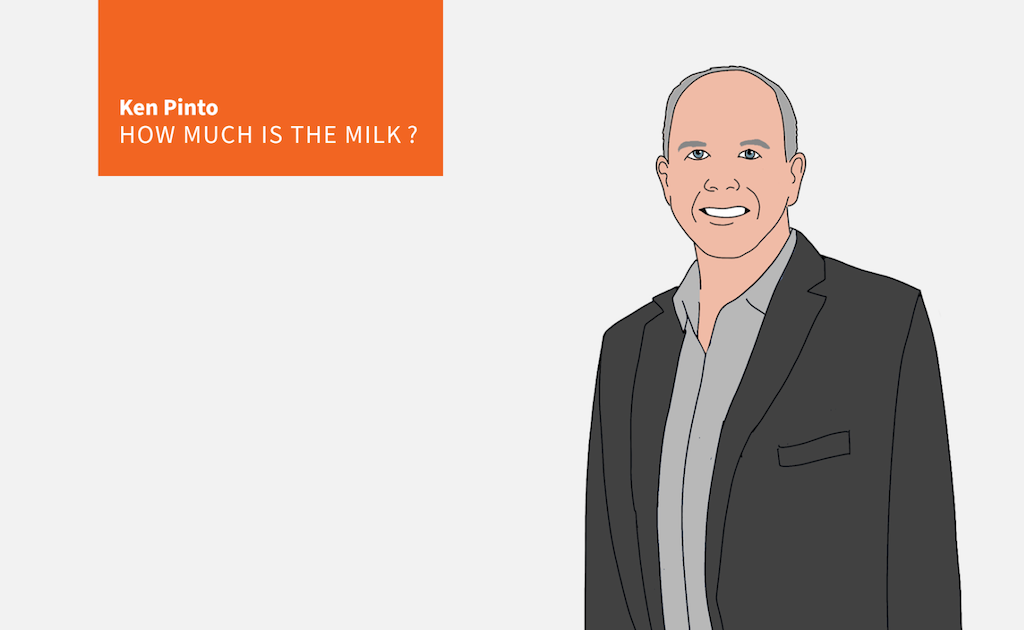
Remember the 90-, or 120-, or even more extra days it took to complete your build cycles and deliver new homes in 2022? No one wants to believe supply chain issues are back, but current chokepoints in the Red Sea and the Panama Canal have shippers scrambling for alternative routes — at a cost.
Since the fall, attacks on ships in the Red Sea by the Iranian-backed Houthis have been disrupting global trade. Meanwhile, severe drought has water levels in the Panama Canal at their lowest point in decades, which has impacted the number and size of vessels that can pass through. According to The Associated Press, total transits through the Panama Canal in December were 36% lower than a year ago and 62% lower than two years ago.
Perfect Storm Redux?
What would – or does – it take for a significant supply chain disruption to impact homebuilding in the United States? Many of the builders I speak with are confident the perfect storm of supply chain constraints in 2021-2022 was a one-off. They say there is no need to prepare for something that will never happen again. However, certain events could play a role in another debilitating break in the supply chain:
- Another virus—could the SARS-CoV2 global pandemic be duplicated with another virus? We have recently dealt with MERS, SARS CoV1, SARS CoV2, and Ebola, and we are now hearing about Disease X and how scientists are preparing for the next pandemic.
- Oil capacity is being toyed with by OPEC, Russia, Venezuela, and the U.S. Can U.S. trucks not get adequate diesel fuel, or maybe the price will be so high it will again necessitate the addition of surcharges to product deliveries?
- War has a way of disrupting supply chains. While those of us in North America may not think our product availability has changed much since Russia invaded Ukraine, the countries that were dependent on food coming from Ukraine surely can feel the pain. Trade routes stand to be disrupted by war in Israel, Iran/Syria/Pakistan, Sudan, North Korea, and, the biggest elephant in the room, Taiwan. I suspect that if or when one bomb drops on Taiwan, the supply chain effect will be both global and colossal.
Despite apparent builder confidence, vulnerabilities in the supply chain have not remedied themselves to the point of no concern. Homebuilders have worked hard to recapture lost construction cycle time, and gain efficiencies. Still, unless there is a continuous effort to harden the flow of materials to be able to withstand such shocks, that hard work is at risk.
The Backstory
In 2021-2022, the world experienced the most remarkable single supply chain constraint in history. During this period—often referred to as the ‘Covid years’—supply chain capacity from raw material suppliers down to end users of building materials saw an increase in demand and a decrease in supply capacity. The result was that some builders did not get the materials they needed when they needed them, which extended construction cycle times far beyond what they promised homebuyers.
If you were lucky enough to find a container to ship your goods, the next hurdle was to book a slot on a container ship. The typical three to five days to get a booking for your container on board a vessel extended to five to seven months, and prices went from $3,500 per container to over $13,000. Ships made so much money bringing goods from Asia to North America that they often returned empty rather than waiting four more days to get loaded with products bound for Asia.
Once your products arrived at the port in California (likely Los Angeles, Long Beach, or Oakland), you might have thought your logistics hurdles were over. Not in 2021-2022. The ports were overwhelmed with the number of ships wanting to offload, partially because of the increased product flow and diminished capacity. The dock workers who manage the ports took precautions to not catch Covid by reducing the days each worker had to be on-site. Fewer equipment operators for cranes, forklifts, and trucks meant less capacity to offload.
The staging areas, used to buffer the flow of containers just offloaded before the truckers could pick them up, were maxed out. This bottleneck frustrated the port's ability to maximize the capacity it had. Truckers were to blame for not picking up the containers fast enough, but the drivers often pointed to the lack of a trailer chassis to go under the container for trucking.
The increased demand for products combined with a shortage of containers, container ships, trailer chassis, trucks, and truck drivers created bottlenecks in the supply chain. China had a similar constraint with chassis, trucks, and truck drivers in its efforts to get products to the ports. And if you thought that rail was an alternative—the unions took this opportunity to renegotiate a labor agreement with the rail companies, which eventually took presidential intervention to conclude.
I often heard people lament, ‘Why don’t they fix the supply chain?’ As if there was only one thing to fix.
Shifts in Supply
Now here we are in 2024. All is well, right? Most logistics constraints have subsided — some due to less demand, and some because of the rapid increase in the construction of containers, trailer chassis, and container ships, all manufactured at a record pace.
New port systems were created to manage ship traffic, allowing ships to wait outside the former 25-mile limit. Now, they can stay off the coast of Mexico, where the weather is a bit warmer. New container ships hold 20,000 to 24,000 TEUs (twenty-foot equivalents), which beats the old average of 15,000 TEUs.
In the past decade, Triton reported an average annual container production of 2.6 million TEUs. In 2021, almost 5.2 million TEUs were manufactured. There is now a surplus of containers and trailer chassis.
The steady flow of products moving around the globe depends on a cadence of ship movement. Today, an average of 115 ships per day are processed in the Long Beach/LA ports, and rarely do they have to wait outside the port. In 2021, the largest container ship, the Ever Given, became lodged in the Suez Canal—it lasted six days at a cost of nearly $10 billion. The Suez Canal is a thoroughfare for goods moving between Asia and Europe.
Homebuilders in North America may not have considered a waterway so far away to have an impact on the ability to acquire the materials needed to build homes. It was only six days, right? However, due to the established flow, this event caused a significant disruption in the movement of container ships, and container availability rippled throughout the globe, causing many tiny bottlenecks managed locally.
Preparation Pays
During the Covid years, some homebuilders leased warehouses and began stocking a buffer of building materials to compensate for the shortfalls they were experiencing. Whether a builder opens up a warehouse or gets more involved in upstream supply chain flow, the need to prepare seems clear. Collaborative inventory management, where the builder and the distributor collaborate on how much inventory to carry, who pays for the extra inventory, and how it gets allocated when needed, will continue to be a best practice in preparing for the next supply shortage. Collaborative inventory management can be accomplished by small and large homebuilders alike.
Materials impacted are those manufactured in a plant—light fixtures, door hardware, appliances, window hardware, faucets, valves, drains, HVAC parts, gas/electric fireplaces, garage door opener parts, and electric wiring parts, to name a few. Lumber, concrete, and drywall are less likely to be affected by a global supply chain disruption, but they are likely to feel logistics constraints on domestic truck and rail operations. Then again, 30% of U.S. cement must be imported from other countries, so it could be an issue, too.
Having the right materials in the right place at the right time is crucial to ensuring you have the right labor in the right place at the right time. Supply disruptions affect builders’ ability to use labor efficiently, leading to more challenges in getting homes built on time.
Builders continue to get bigger through M&A activity, and some believe that the size of the company will guarantee its ability to get materials when others cannot. While that may prove true in some markets and with some homebuilders, the best-run supply chain in the country is not a top-20 builder. In this case, collaboration, not chest pounding, is the key to success.
MORE IN Products
How Precision Can Shave Time From Homebuilders' Build Cycle
Sales may be priority No. 1 right now. And that needs to be bolstered by virtually flawless operations. Boise Cascade’s SawTek gives builders speed, savings, and first-time-right quality when it matters most.
In Uncertain Times, Capability Investment Is A Survival Tool
Boise Cascade’s $140M mill improvements reflect a long-game commitment to builders under pressure from volatility, costs, and customer hesitation.
Margins Tighten, Value-Add Matters In Construction Supply
Even as overall construction supply revenues inch upward, Webb Analytics’ deep dive into the $600B pro channel reveals a shifting reality: declining unit volume, cautious outlooks, and strategic bright spots in value-added manufacturing and service partnerships.