Technology
Reframing What’s Possible: A Housing Factory On The Move
With its 2025 Ivory Prize win, Reframe Systems moves from a promising innovation to a validated force in reshaping housing affordability through modular microfactories, climate-resilient design, and workforce reinvention.
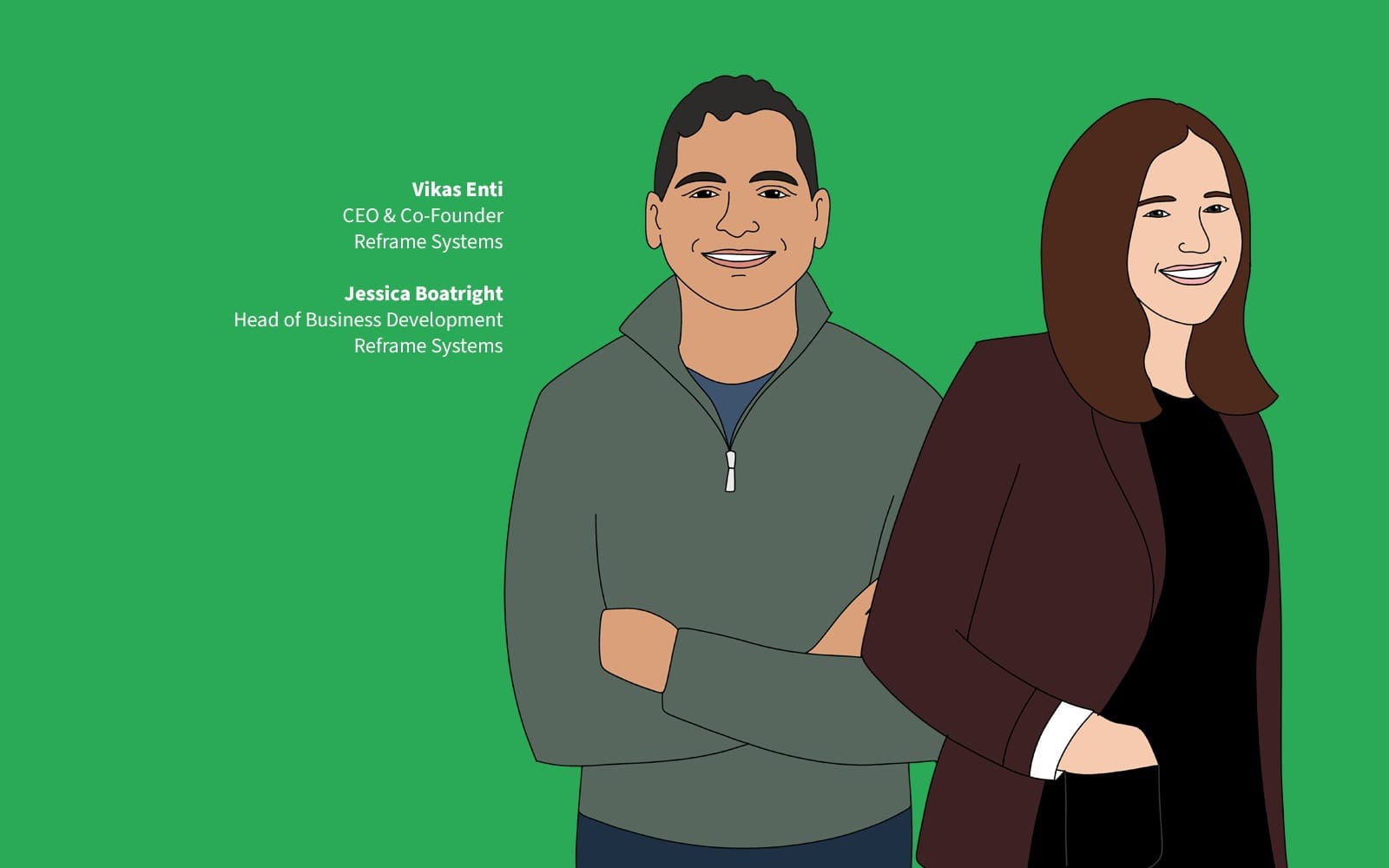
American housing’s fault lines have never, in our memories, been more visible, nor more daunting.
Mortgage costs, insurance premiums, zoning pushback, and a missing generation of skilled labor keep even the most capable builders on defense. Layer in climate risk and a growing affordability gap, and you have a system that isn't just strained— it's fundamentally misaligned with the realities of who needs housing, where, and why.
Reframe Systems, winner of the 2025 Ivory Prize for Housing Affordability in Construction & Design, is not trying to patch over those problems.
It’s trying to rewire the system, one that's shorted out.
We created Ivory Innovations to combat the widening housing affordability gap by recognizing and funding real-world solutions that are addressing this growing crisis,” said Clark Ivory, CEO of Ivory Homes and founder of Ivory Innovations in a provided statement. “The 2025 Ivory Prize winners are bringing to market visionary approaches that push the boundaries of what’s possible in making housing more affordable. Through collaborative policy reform, groundbreaking construction approaches and innovative financial solutions, these leaders are turning the tide on one of our country’s most pressing challenges—housing affordability.”
Founded by robotics veterans from Amazon and led by CEO Vikas Enti, Reframe isn’t just betting on automation or off-site modular housing. It’s designing and deploying low-cost micro-factories that build airtight, climate-ready homes closer to where people need them with a product platform aimed and economically modeled squarely at the missing middle—urban infill, scattered-site redevelopment, and ADUs—Reframe.
It's faster and better, but it also offers an answer to how fairly ground-up home development can be done.
Ivory Prize Honors: A New Chapter, Not a Culmination
The $100,000 Ivory Prize honor doesn’t just add to Reframe’s credibility. It’s already moving the work forward. This summer, one of the company’s first two homes headed to wildfire-damaged Altadena, CA, will be partially subsidized by the Ivory award money, serving as both a model and a message: that cost, speed, and climate resilience can coexist.
We're using the Ivory Prize to do exactly what it's intended for," Enti says. "We're proving that there's a better way to rebuild, starting in one of the most difficult housing environments in the country."
Reframe’s model flips the typical offsite construction playbook. Instead of investing $30 to $50 million in a centralized facility and hoping demand shows up, Reframe builds only when there's a minimum $10 million pipeline of secured demand.
In other words, it can scale as a capital-light investment model, and prove itself rapidly as a sustainably profitable operational business model. That's a rare thing!
Its current Massachusetts facility costs less than $5 million and is already on track to deliver 20 homes this year.
From a social and political standpoint, modular can’t scale in high-cost areas unless it’s tied to local investment and job creation," says Jessica Boatright, co-founder and head of business development at Reframe Systems. "That’s what makes our microfactory model so powerful—it’s designed to meet local needs, not just ship product from afar.”
These numbers starkly contrast with the origin-to-operational profitability trajectories of dozens of vaunted housing automation, robotics, and industrialization initiatives that raised hundreds of millions of dollars in investment capital only to fall by the wayside in the past handful of years.
A Wildfire Rebuild Blueprint, With California In Sight
With microfactory deployment possible in under 100 days, Reframe is preparing a second facility for Southern California. But the expansion is disciplined.
We never want to speculatively build a factory," Enti says. "Our non-negotiable is: demand first."
The two Altadena homes will serve as real-world proofs in a market that demands fire-rated assemblies, updated Wildland Urban Interface specs, airtight envelopes, and compliance with seismic and wind-load codes. However, the rebuilding challenge is more than regulatory. Homeowners often find insurance payouts fall short of actual rebuilding costs. To address this, Reframe is partnering with local banks to structure CRA-aligned bridge financing that fills the gap.
If that model works, Reframe expects to trigger the development of a local factory by early 2026.
Modular Without Short-Cuts: Lessons from Triple Deckers
While California planning advances, Reframe is refining its modular platform through its triple-decker infill projects in Somerville, MA. Two three-story buildings—comprising 28 factory-finished volumetric modules—are under construction this spring.
The homes are virtually identical in form, but serve different purposes. One is for a nonprofit developer offering 50% AMI rentals. The other is a multigenerational home for a local family. Same structure, same specs, different financial models.
High quality doesn’t have to mean luxury," Reframe's Boatright says. "And just because it’s affordable doesn’t mean it should feel temporary. We’re proving that resilient, beautiful homes can serve both market-rate and subsidized buyers with no compromise.”
This is central to Reframe’s thesis.
We don’t differentiate the product," Enti says. "We simplify the supply chain and use the same system whether it’s market-rate or affordable. That keeps quality high and pricing predictable."
The logistics rethink goes beyond the factory. Smaller boxes mean smaller cranes and easier navigation through narrow city streets. Pre-staging is simulated digitally, and modules arrive with appliances, plumbing, and finishes installed. What would typically be a six- or eight-box structure now arrives in 28 discrete, optimized pieces.
Superpowered Apprentices: A New Workforce Model
Inside the factory, Reframe is redefining the talent pipeline. Of its current team, 60% are novices or technical high school students in co-op programs. None are traditional journeymen. That’s by design.
Our software, vision systems, and workflows let people new to the trades do highly skilled work in days or weeks, not years," Enti explains. "And we want them to eventually afford the homes they’re building."
As Reframe expands, the goal is to increase novice participation to 90%. The goal isn’t just headcount. It’s to create a scalable, repeatable workforce solution in a sector that is hemorrhaging skilled labor.
A Business Model Built for Mixed Markets
Reframe operates as both builder and co-developer. Its triple-decker model offers units that qualify for both public subsidy and open-market pricing. In one upcoming 12-home Massachusetts development, three units must be deed-restricted affordable. Reframe’s approach eliminates the common developer challenge of needing different designs and finishes for different price tiers.
This uniformity also avoids the zoning, permitting, and neighborhood friction often caused by visible differences between subsidized and market-rate housing.
Still, the model is not without friction. Some subsidized housing agencies have questioned whether Reframe’s higher-quality finishes might bring higher long-term maintenance costs. Enti acknowledges the concern but argues the opposite:
We're confident the materials are durable and reduce maintenance over time. But we listen, and we’re learning."
Scaling to LA, and Then?
Enti says that within the next year, Reframe will deliver its 20-home New England plan and complete its Altadena projects. If demand aligns and financing tools unlock, the next step is launching a Los Angeles-area microfactory — proof not just of production capacity, but of Reframe’s ability to scale and serve in disaster-prone, high-cost regions.
But perhaps Reframe’s biggest contribution is conceptual: showing that housing production can be fast without being cheapened, local without being small-scale, and affordable without compromising dignity, performance, or aesthetics.
If there were one lever I could pull," Enti says, "it would be guaranteed permitting timelines. That’s the friction point that kills too many good projects. The rest — financing, technology, factory deployment—we can figure out."
That may be Reframe’s most radical idea: that the hardest parts of housing can be solved not by one silver bullet, but by removing the invisible barriers that keep good ideas from moving forward. With the Ivory Prize as fuel and two coasts now in view, Reframe is betting that scalable resilience and local trust can go up in less than 100 days—and last a lifetime.
MORE IN Technology
Faster Lots, Lower Costs, Fewer Mistakes: Elevating Site Intel
Margins are under pressure, and inefficiency is expensive. We explore how builders are using tech like TraceAir to speed up site work, eliminate rework, and stay on budget — even when everything else feels uncertain.
When Homebuyers Freeze, Homebuilders Must Build Their Machine
New-home demand is sputtering as buyers second-guess timing, costs, and rates. Our upcoming webinar with Signature Homes and Higharc explores how builders can reset the rules with customer-first systems.
No Pit Stops: Homebuilders Must Pivot And Retool In Real-Time
Among homebuilders, survival now means a “both-and” approach—combining short-term tactics with long-term digital transformation. Here’s why builders must shift from siloed workflows to connected systems without waiting for recovery.