Building Resilience
Rebuilding After Fire: Can Hempcrete Help Future-Proof Homes?
Los Angeles grapples with rebuilding after January’s devastating fires. One Idaho company thinks hemp-based materials could be the future of resilient home construction.
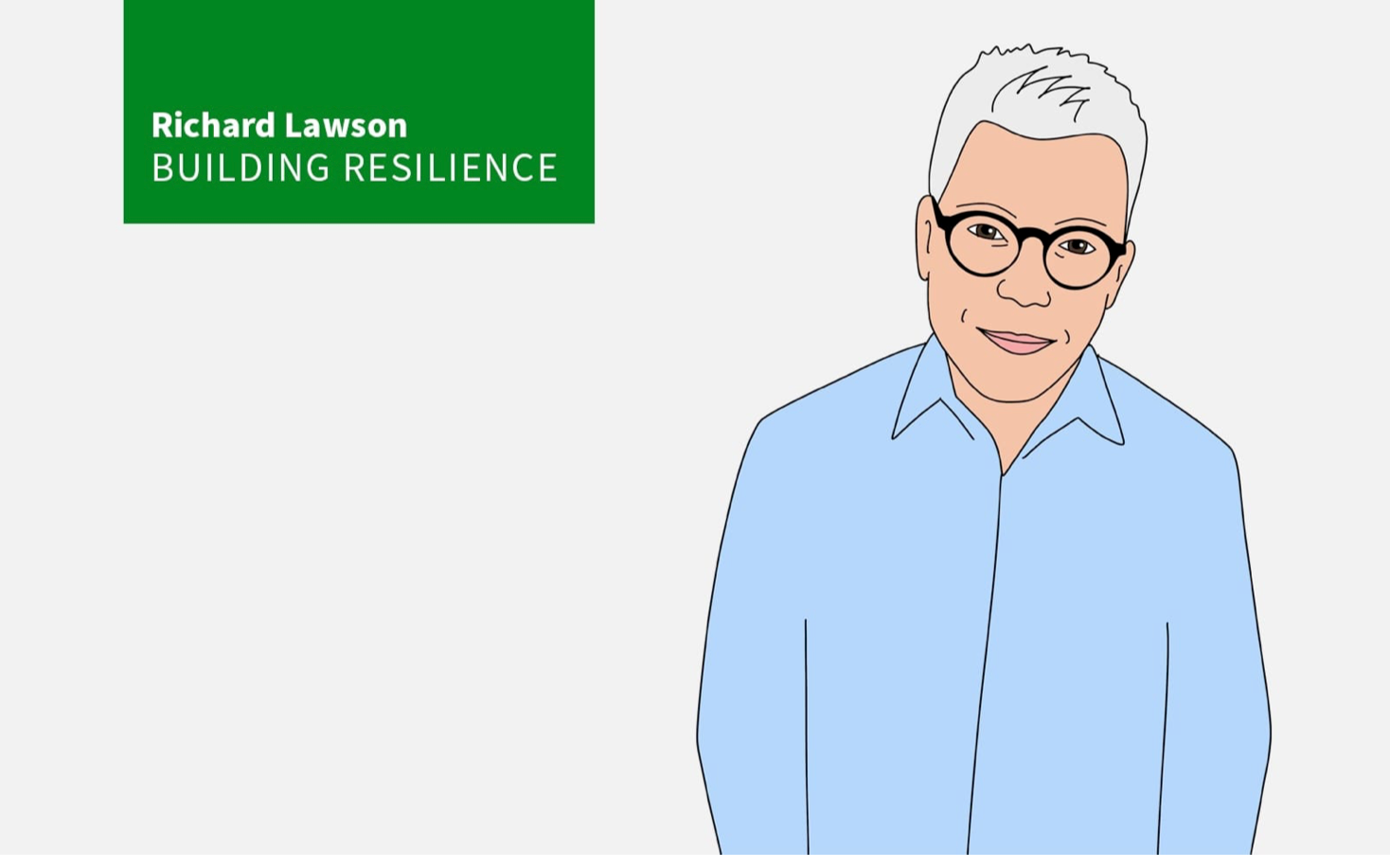
[Editor's note: Wildfires in Los Angeles. Hurricanes across Florida and the Southeast. Floods, extreme heat, and severe weather events are no longer rare occurrences—they’re becoming the new normal. The homebuilding and residential development industries face an urgent reckoning: how to build homes, neighborhoods, and communities that can withstand the increasing severity of climate-related natural disasters. This interview is another installment in a series from The Builder’s Daily exploring the choices, challenges, and solutions shaping the future of resilient housing.]
Only a handful of homes have received permits to rebuild or repair damage in Los Angeles and the surrounding county since the devastating fires were contained in late January, drawing criticism from local politicians.
While the city and county grapple with expediting permitting, debris removal continues. It’s been a massive undertaking, including recycling debris from more than 16,000 homes and structures.
Builders and suppliers have been lining up to help homeowners build back with resiliency to withstand the next fire. Concrete panels, concrete blocks and steel framing are among the available fire-resistant materials.
In addition to these alternatives, industrial hemp is emerging as an option. Ketchum, Idaho-based Hempitecture, which makes and sells industrial hemp building products, recently opened a fulfillment hub in Los Angeles.
Hemp might not seem fire-resistant intuitively. However, Hempitecture’s hempcrete — a mix of hemp and lime — has been tested to the ASTM E84 standard and proven to be 100% fire-resistant.
Hempcrete can coat wood framing for protection, and hemp blocks and pads are used for insulation.
Like other resilient and sustainable products, Hempitecture products sell at higher prices than traditional building materials. The selling point is that these products, while higher on the front end, save money in the long run through lower insurance costs because of less fire risk and lower energy usage.
We are on the cusp, or maybe even in the midst, of a paradigm shift in thinking about the value of our homes in light of what's happened in Southern California and insurance becoming a huge issue,” says Mattie Mead, who co-founded Hempitecture in 2013. “Strategies and building materials that are more resilient and proven to be more resilient, you might still pay an upfront premium, but that premium can pay dividends down the line, through a more insurable product. We will see homes and projects be rebuilt in conventional stick frame typologies and building methodologies, but we do hope that folks will look toward more resilient building methods, even if there is a price delta.”
Scale is key to any of the resilient products. Greater adoption helps bring prices down.
As we grow and scale and expand to more regions, we can improve our value proposition, just in terms of cost through accessing that scale, which is another reason why being located in Southern California, which historically has been such a great market for us, continues to be even more important today,” Mead says. “Our plan is growth, and with growth, we could take advantage of better buying opportunities for our raw material commodities, driving down the cost and tapping into operational efficiencies.”
Hemp Growth
Varying quantities of industrial hemp grows in all states across the U.S. Texas led the country last year in planting, with 4,900 acres, a 1,860% increase over 2023, according to a U.S. Agriculture Department report.
Hemp had been on the federal controlled substances list since 1970, no matter how low the THC level. The 2014 Farm Bill created an exemption for states to establish pilot programs for hemp research by universities or state agriculture departments on using hemp that contained less than .3% THC.
The 2018 Farm Bill removed hemp from the controlled-substance list, helping the agricultural product flourish. By then, more than 40 states had established pilot programs.
Hemp requires less water and fewer pesticides than cotton or other major crops. Its natural pest resistance reduces the need for chemical treatments, lowering environmental pollution and input costs. It also grows quickly, maturing in months, in contrast to the decades trees used for lumber require.
Hemp is now used in making flooring products, furniture and cabinets.
Environmental Challenge Caused by the Fires
Many of the homes that burned were “aging stock,” and tended to contain asbestos and lead paint. Lithium-ion batteries in electric vehicles blew up. It all served as a recipe for toxic ash and debris that littered the ground and air.
The EPA cleaned up the ground quickly. Still, toxic ash infiltrated many of the homes that survived. Owners of those homes told 60 Minutes recently that they worry about the cleanup within their homes.
Ensuring fewer toxins in their homes is on the minds of those building back. It’s on the new homebuyers across the country who are demanding more eco-friendly construction.
As folks in Southern California and beyond look to building back and restoring their neighborhoods and communities, they're going to think more about resiliency,” Mead. “And resiliency can be tied together with not just sustainability, but also health.”
And focusing on health means building with fewer synthetic materials. In a sense, many of the methods considered resilient and sustainable mark a return to building methods of yore.
Building with the Earth is a tale as old as humanity,” Mead said. “All shelter was built with earthen, natural materials. We're putting materials into homes that are grown from the earth and born from the earth and actually manufactured with renewable energy.”
MORE IN Building Resilience
Los Angeles Halts SB 9 Light-Density Housing in Fire Zones
Los Angeles’ emergency order blocks Senate Bill 9 lot-splits in fire-ravaged Pacific Palisades, restoring the single-family pattern that existed before the January inferno. The move underscores tensions between state housing law and local disaster realities.
LA Rebuilds Come With Terrain, Code Costs Hiding In Plain Sight
Wildfire survivors in Los Angeles now face a second blow: costly landslide safety mandates and soaring insurance premiums, threatening the future of generational neighborhoods. TBD's Richard Lawson reports.
Building For Tomorrow Today: Neighborhood Scale Resilience
How IBHS’s Fred Malik and the FORTIFIED program are redefining risk, reshaping design, and restoring trust through science-backed, community-wide resilience. Malik takes a deep dive into the issues and implications for builders with contributor Richard Lawson.